Preliminary findings of ECHO research
This article summarizes work being done at ECHO in Florida to develop a method for small-scale farmers and community seed banks to make their own desiccant to dry and preserve seeds. The three main requirements are clay, wood ash, and a way to heat the beads. Wood ash is a common byproduct of wood-burning cookstoves, and clay can be obtained from clay soil found in many parts of the world. Heating can be done with a forge used by local blacksmiths.
Introduction
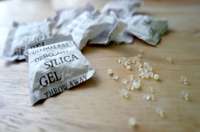
Figure 15. Silica gel as an example of a desiccant. Source: FREEPIK
A desiccant is a hygroscopic drying agent. Hygroscopic substances take up and retain moisture from the air. There are many types of desiccants including molecular sieves, activated alumina, activated carbon, bentonite, calcium sulfate, montmorillonite clay, calcium chloride, zeolite, and silica gel (Cohen, 2000; SorbentSystems, 2022; Figure 15). Desiccants have many everyday functions from absorbing moisture from a damp room in your home, keeping electronics dry, to drying freshly harvested seeds for long-term storage.
Desiccants to dry seeds for seed preservation
There are many methods to dry seeds. Examples include hanging seeds from trees, drying seeds in the sun, using desiccants, using simple local driers, drying seeds on tarps, drying seeds on curing tables, and using wood ash (Chua and Chou, 2003). Methods used to dry seeds have evolved over time with indigenous knowledge and advances in agricultural technologies (Matsa and Mukoni, 2013; Shaila and Begum, 2021). We now know the seed drying process is vital to a seed’s emergence and crop productivity (Harrington, 1959; Saipari et al., 1998). For this reason, many seed banks and home gardeners use desiccants like silica gel or zeolite (drying beads) to absorb moisture from freshly harvested seeds and reduce humidity in storage containers. Drying capacity varies between desiccants and is influenced by the ratio of seeds to desiccant in a container. Placed in airtight containers, desiccants can typically dry seeds to a moisture content of 10% or less.
Why not just buy desiccants?
Desiccants like silica gel and zeolite are effective for removing moisture from seeds and reducing fluctuations in seed moisture content over time. However, these products are not readily available in low-resource settings. It may be difficult for a smallholder farmer or rural community seed banks to purchase and ship desiccant from another region or country. Some materials, like rice or salt, are more available, but have competing household uses. A product that farmers can make themselves addresses issues of cost and availability.
How a locally made desiccant could compliment traditional practices
Many smallholder farmers use containers like gunny bags, mud bins, clay pots, bamboo structures, wooden bins, underground structures, and in woven bags hung near stoves or from trees to store seeds (Wright and Tyler, 1994). Such containers have been used by farmers for generations and are readily available. These containers differ in their porosity. Some, like gunny bags or sisal sacks, have large holes and are not airtight. Under warm, humid conditions seeds kept in porous containers are subject to mold, resulting in reduced viability and increased risk for aflatoxin contamination (Bankole et al., 2004). With traditional open storage, seed moisture levels have been shown to fluctuate by 2% to 3% over a 12 month storage period (Rickman and Aquino, 2004). Other traditional containers are less porous or can be modified to exclude humid air more effectively. Clay pots are often made with a top or lid that can be sealed with mud or clay. Pots and bins can also be lined with plastic. More examples of commonly available, less- or non-porous containers include tin cans, plastic or glass bottles, and polyethylene bags.
Seeds remain viable for longer periods of time in airtight containers than in those with large holes. In Ethiopia, for example, the germination percentage of Oxytenanthera abyssinica (a species of bamboo) seeds after 12 months of storage was 70% or higher with tin cans and glass bottles, but only 7% with sisal sacks (Ayana et al., 2012). In their work with French bean (Phaseolus vulgaris), Khalequzzaman et al. (2012) found that the incidence of seed storage fungi (Fusarium oxysporum) was lower with the seeds kept in tin cans than in gunny bags. Remember that seeds placed in a sealed container need to be dry to begin with, to keep from trapping moisture in the container.
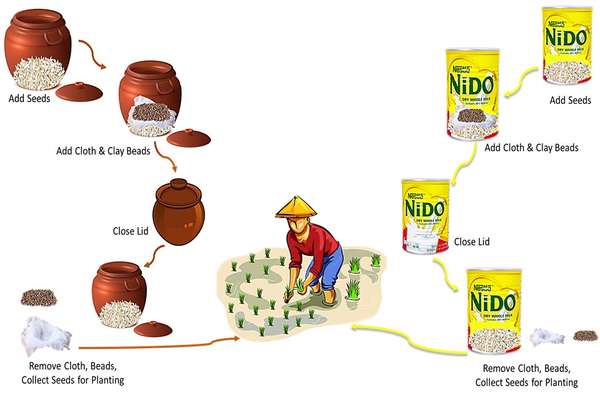
Figure 16. Illustration of clay-bead desiccant in pots (left) and tin cans (right). Source: Guinevere Perry
Desiccant placed in open containers will be quickly saturated with moisture under humid conditions. A desiccant will dry seeds faster and keep them dry for a longer period if placed in a closed container that is as airtight as possible. The clay beads ECHO has been working with can easily be added to clay pots, tin cans, and glass or plastic bottles (Figure 16). Some closed containers are not perfectly sealed. Even glass jars are not completely airtight if the lids do not seal well. In such cases, keeping some desiccant with the seeds, in their storage containers, will help keep seeds dry. If using well-sealed containers, a farmer could 1) use the desiccant to dry seeds initially and then remove it or 2) keep the desiccant with the seeds if she/he will need to open the container from time to time to access the seeds.
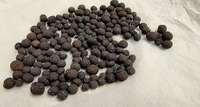
Figure 17. Beads made with a mix of clay and wood ash. This is what they look like after they have been heated. Source: Guinevere Perry
How do we make clay beads?
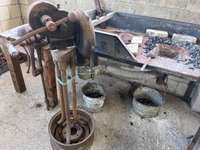
Figure 18. Forge used at ECHO to heat beads made with clay and wood ash. Source: Tim Motis
We start by extracting clay from soil that has a lot of clay in it to begin with. The beads will hold together best if the clay is free of other particles like sand. We then combine clay, wood ash, and water to form small clay balls. The resulting beads are heated until they glow red or orange, which happens at a temperature of 600 to 800°C. This heating process is known as calcination. Calcination converts calcium carbonate to calcium oxide, giving the clay balls (Figure 17) their absorbent property. We have found that a forge (Figure 18) typical of that used by blacksmiths can heat the beads to temperatures of over 600°C. The above-mentioned video shows how we heat beads placed in a stainless-steel bowl,6 with the bowl covered (by a second stainless steel bowl of equal size; this keeps debris from contaminating the beads) and surrounded by charcoal. Safety is an important aspect of the heating process. Use tongs and do not touch the beads until they have cooled.The next section on in-house testing contains information on how much wood ash to mix with the clay.
In-house efficacy testing
We have been experimenting with clay beads to validate their effectiveness. We have been working to identify the optimum formulation, optimum heating temperature and time, and optimum shape and design. Initial trials started in January 2023 and are ongoing. There have been several versions of clay beads with varied performance capabilities (Figure 19).
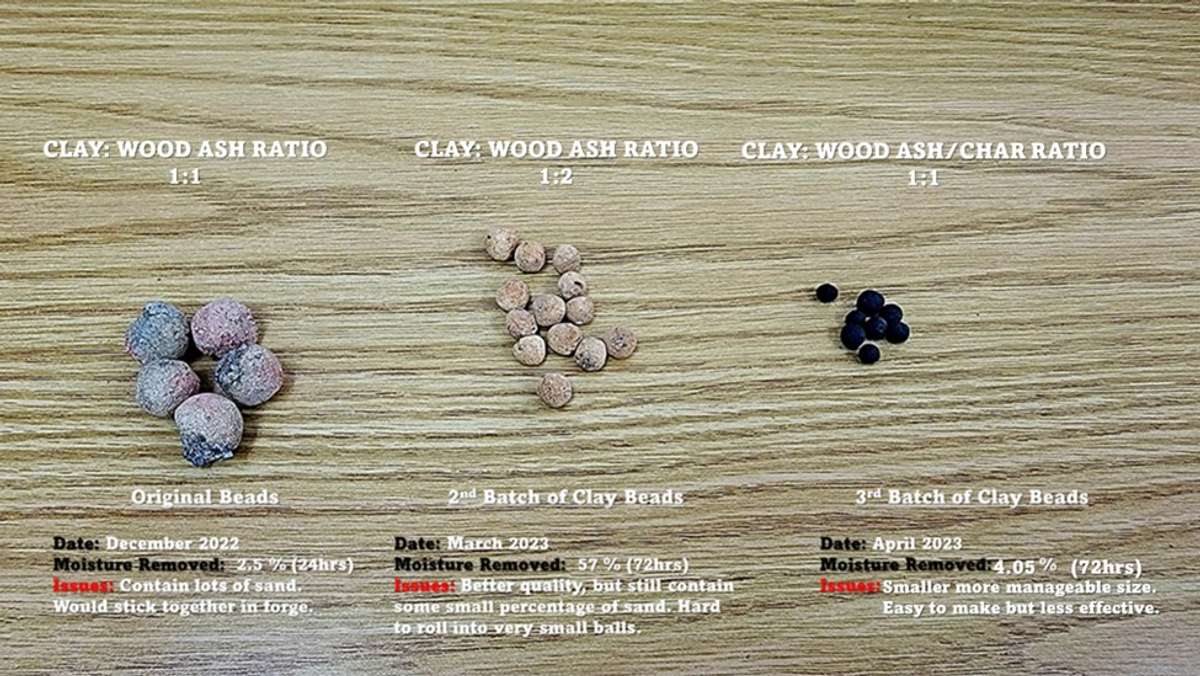
Figure 19. Clay beads and their effectiveness at several ratios of clay to wood ash. Source: Guinevere Perry
Beads of the third batch in figure 19, made with a 1:1 ratio of clay: wood ash, were tested to determine if the clay beads could be reused by heating the beads at a low temperature for a short duration of time without reducing prior performance. The beads were placed in mason jars with cowpea (Vigna unguiculata) seeds for 24 hours. After 24 hours we measured the moisture content of the cowpea seeds and heated the clay beads at 120°C for 10 minutes to remove moisture. We then placed the reheated beads in a mason jar with a new set of cowpea seeds and repeated the test five times with duplicate samples. Each set of cowpea seeds had an initial moisture content of 12 to 15%. Table 4 shows results of the five tests. Negative values indicate the percentage of moisture lost from the seeds while positive values indicate the percentage of moisture gained.
Test | Negative Control (no desiccant) * | Positive Control (Zeolite - Drying Beads®) * |
ECHO Clay Beads (1:1 clay to wood ash ratio) * |
---|---|---|---|
1 | -0.21 | -2.62 | -1.35 |
2 | -0.22 | -2.44 | -1.27 |
3 | -0.2 | -2.82 | -1.35 |
4 | +0.03 | -2.37 | -1.15 |
5 | -0.85 | -3.08 | -2.05 |
Standard deviation | ± 0.33 | ± 0.29 | ± 0.35 |
*Negative values show the percentage of moisture removed from cowpea seeds while a positive value indicates the percentage of moisture gained. | |||
**Tests were run with 20 g of cowpea seeds added to each of two jars per treatment. The negative control jars contained no desiccant while those for the positive control and clay beads contained 20 g of desiccant along with the cowpea seeds. |
With no desiccant, the moisture content of cowpea seeds changed little each time. We observed the highest moisture losses (negative values) with zeolite Drying Beads®; however, the clay beads effectively removed moisture from the cowpea seeds after being reused for at least five times.
Conclusion
Clay beads are very cheap to make. Clay and wood ash are already present on many farmsteads and would cost virtually nothing except the time needed to gather them and remove impurities from the clay. The beads work in high humidity, absorb moisture from the air, and reduce seed moisture content. The most limiting factor to making clay beads is perhaps a means to heat the beads. The initial heating could be done by local blacksmiths or homemade forges. Our trials indicate that you can reuse clay beads a minimum of five times and still maintain efficacy. This may mean a farmer could use the beads for several years before needing to discard them. They can be reactivated by exposure to 120°C to 200°C for 8 to10 minutes. However, remaining questions include:
- How important is the source of wood ash?
- To what extent do differences in clay soils affect the stability and performance of the beads?
- To what extent can the beads be reused if they reach the point where they can no longer absorb moisture before being reheated?
- During the heating process, how long should heating continue once the clay beads glow orange or red? Our best results have been with beads heated for 20 minutes once the temperature exceeds 800°C. The total processing time is usually 30 minutes.
- Are there ways, other than a forge, to heat the beads initially? Options to consider include rocket stoves or grills. Aim for an approach that allows you to reach a temperature high enough for calcination with as little fuel (e.g., wood, charcoal) as possible.
- As with any innovation, we encourage you to experiment with local materials to come up with a product that is reproduceable and appropriate for your context. Please let us know of your experience with this or other seed drying approaches.
References
Ayana, D. A., Z. Tadesse, and Y. Kebede. 2012. Effect of storage media and storage time on germination and field emergence of Oxytenanthera abyssinica seeds. International Journal of Basic and Applied Science, 1(3), 218-226.
Bankole, S. A., O.A. Lawal, and A. Adebanjo. 2004. Storage practices and aflatoxin B1 contamination of ‘egusi’ melon seeds in Nigeria. Tropical Science, 44(3): 150-153.
Chua, K. J., and S.K. Chou. 2003. Low-cost drying methods for developing countries. Trends in Food Science and Technology, 14(12): 519-528.
Cohen, A. P. 2000. Desiccants. Kirk Othmer Encyclopedia of Chemical Technology.
Harrington, J. F. 1959. Drying, storage, and packaging seed to maintain germination and vigor. Proceedings Short Course Seedsman, 89-108
Khalequzzaman, K. M., M.M. Rashid, M.A. Hasan, and M.A. Reza. 2012. Effect of storage containers and storage periods on the seed quality of French bean (Phaseolus vulgaris). Bangladesh Journal of Agricultural Research, 37(2):195-205
Matsa, W. and M. Mukoni. 2013. Traditional science of seed and crop yield preservation: exploring the contributions of women to indigenous knowledge systems in Zimbabwe.
Rickman, J. F. and E. Aquino. 2004. Appropriate technology for maintaining grain quality in small-scale storage. In: Proceedings of the International Conference on Controlled Atmosphere and Fumigation in Stored Products. (Donahaye, E. J., Navarro, S., Bell, C., Jayas, D., Noyes, R., Phillips, T. W. eds.). p. 149-157.
Saipari, E., A.M. Goswami, and M. Dadlani. 1998. Effect of seed drying on germination behaviour in citrus. Scientia Horticulturae, 73(2-3):185-190.
Shaila, M. and N. Begum. 2021. Ancient farming methods of seed storage and pest management practices in India - A Review. Plant Arch, 21:499-509.
SorbentSystems 2022. Desiccant types. IMPAK Corp. https://www.sorbentsystems.com/desiccants_types.html
Wright, M. and P. Tyler. 1994. Traditional seed-saving practices in northern Ghana and central Malawi. Chatham: Natural Resources Institute.