This article is from ECHO Asia Note #19 บทความนี้มาจาก สารเอคโค ฉบับที่ 19
[บรรณาธิการ: เนื่องจากความนิยมที่เพิ่มขึ้นเกี่ยวกับแหล่งที่มาพลังงานทางเลือกและพลังงานทดแทนที่ได้มาจากการทำการเกษตร เราจึงได้รับคำสอบถามมากมายเกี่ยวกับการนำก๊าสชีวภาพจากการทำการเกษตรไปใช้เพื่อเป็นพลังงานสำหรับเครื่องจักรขนาดเล็ก บทความนี้มีจุดประสงค์ที่จะกล่าวถึงหนึ่งในความเป็นไปได้หลายๆทางในการใช้ก๊าสชีวภาพที่ได้จากมูลสัตว์ เพื่อเป็นพลังงานสำหรับเครื่องยนต์ดีเซลขนาดเล็ก]
คำนำของผู้เขียน
ชุมชนชนบทห่างไกลหลายแห่งที่มีเจ้าหน้าที่ของสถาบัน LIRE อาศัยอยู่นั้นเป็นพื้นที่ที่ห่างไกลความสะดวกสบาย เช่นพื้นที่ที่ไม่มีไฟฟ้าใช้ และงานพัฒนาชุมชนงานแรกที่ผมได้รับมอบหมายก็อยู่ในชุมชนแบบนั้น คือที่โรงพยาบาลห่างไกลแห่งหนึ่งทางตอนเหนือของกรุงเวียงจันทน์ สาธารณรัฐประชาธิปไตยประชาชนลาว ถึงแม้ที่นั่นจะตั้งอยู่ห่างไกล แต่ก่อนหน้านั้นไม่นานโรงพยาบาลนี้ได้ติดตั้งบ่อหมักก๊าสชีวภาพแบบฝังดินขนาด 10 ลบ.ม. เพื่อใช้สำหรับการหุงหาอาหารให้กับโรงพยาบาลและบ้านพักของแพทย์ เชื้อเพลิงที่ใช้มาจากวัว 20 ตัวที่เป็นของโรงพยาบาล และทางโรงพยาบาลยังมีเครื่องยนต์ดีเซลขนาด 10 กิโลวัตต์ ซึ่งเป็นเครื่องยนต์ขนาดเล็กที่ผลิตจากประเทศจีน และใช้เชื่อมต่อกับเครื่องปั่นไฟแบบเฟสเดียวเพื่อให้แสงสว่างและใช้ชาร์ตโทรศัพท์มือถือเป็นระยะเวลา 2-3 ชั่วโมงในตอนเย็น
งานที่ผมต้องทำคือใช้ก๊าสที่ได้จากบ่อหมักก๊าสชีวภาพเพื่อเดินเครื่องยนต์ดีเซล จึงเป็นที่มาของโครงการที่ในช่วงแรกผมรู้สึกท้อแท้แต่ในเวลาเดียวกันก็ทำให้ผมมีความเข้าใจและได้เรียนรู้มากขึ้น ในฐานะตัวแทนของมูลนิธิ FACT (http://www.fact-foundation.com ในเวลาต่อมาผมได้ดำเนินโครงการที่เป็นการต่อยอดจากโครงการคที่ผมได้ทดลองทำในเบื้องต้น. ในบทความนี้ ผมจะเขียนเกี่ยวกับบทเรียนต่างๆที่ผมได้รับจากขบวนการทำงาน จึงไม่มีอะไรที่เป็นตัวเลขที่ชัดเจนหรือมีความถูกต้องทางวิทยาศาสตร์ 100 เปอร์เซ็นต์ แต่เป็นเพียงประสบการจริงที่ผมได้เรียนรู้จากการทำการทดลองในสถานที่ที่ห่างไกล และมีข้อจำกัดด้านวัสดุอุปกรณ์ และนอกจากนี้ผมได้พยายามหลีกเลี่ยงการใช้คำศัพท์เฉพาะทางวิชาในการเขียนให้ผู้อ่านเข้าใจได้ง่าย
สาระสำคัญ
การเดินเครื่องยนต์ดีเซลด้วยก๊าสชีวภาพนั้นมีความเป็นไปได้แน่นอน แต่อย่างไรก็ตาม ต้องมีการคำนึงถึงปัจจัยที่เกี่ยวข้องต่างๆก่อนที่จะนำไปเป็นทางเลือกสำหรับโครงการพัฒนา บทความนี้จะช่วยในการสำรวจปัจจัยและข้อคำนึงที่สำคัญๆเมื่อต้องการใช้ก๊าสชีวภาพในเครื่องยนต์ดีเซล
ข้อมูลเบื้องต้น
ความสำคัญประการแรก คือ การแยกความแตกต่างระหว่างเครื่องยนต์ดีเซลชนิดต่างๆ เครื่องยนต์ดีเซลนั้นค่อนข้างจะมีความคล้ายกันในการเดินเครื่องและมีมาตั้งแต่ที่รูดอล์ฟ ดีเซลได้สร้างเครื่องยนต์ขึ้นครั้งแรกในช่วงปี ค.ศ. 1800 ซึ่งเครื่องยนต์นี้ต้องอาศัยการจุดระเบิดด้วยการอัด (Compression Ignition หรือ IC) ด้วยการที่น้ำมันดีเซลจำนวนหนึ่งถูกฉีดเข้าไปที่ห้องเผาไหม้เครื่องยนต์ ซึ่งมีวาล์วคอยเปิดออกเพื่อให้อากาศเข้าไปในห้องเผาไหม้นี้ วาล์วนี้จะถูกปิดและลูกสูบจะบีบอัดอากาศกับเชื้อเพลิง เมื่ออากาศกับเชื้อเพลิงนี้ไปถึง “จุดเผาไหม้ที่สมบูรณ์” (เช่น จุดที่อัตราส่วนระหว่างเชื้อเพลิงต่ออากาศพอเพียงในการเผาไหม้) ก็จะเกิดการติดไฟภายใต้แรงดันที่เกิดขึ้นเมื่อลูกสูบเคลื่อนไปที่ตำแหน่งบนสุด (Top Dead Centre หรือ TDC) ซึ่งมักอยู่ที่อัตราการอัดราวๆ 17:1 ขณะที่เกิดการจุดระเบิด ลูกสูบจะถูกผลักลงด้านล่างทำให้ก้านสูบเคลื่อนและทำให้เครื่องยนต์ทำงาน รถยนต์ที่เป็นเครื่องยนต์ดีเซลสมัยใหม่มีระบบเชื้อเพลิงและระบบการจัดการเครื่องยนต์ที่ซับซ้อนที่ทำให้เครื่องยนต์มีประสิทธิภาพสูงมากแต่ก็ค่อนข้างที่จะ “มีปัญหาง่ายกว่า” การนำก๊าสที่ไม่บริสุทธิ์ (เช่นก๊าสชีวภาพ) มาใช้ทดแทนนั้นจึงอาจส่งผลให้เกิดปัญหาได้
เครื่องยนต์ขนาดเล็กที่ใช้แทนแรงงานสัตว์ที่พบได้ทั่วไปในเอเชีย หรือเป็นที่รู้จักกันคือควายเหล็กหรือรถไถนา เป็นการออกแบบที่ง่ายกและไม่ซับซ้อน นอกจากนี้ยังมีระบบหัวฉีดเชื้อเพลิงธรรมดาแบบ “คอมมอนเรล” หรือระบบปั้มแรงดันสูง และมีธรรมดายิ่งกว่านั้นคือเครื่องยนต์ของลิสเตอร์ (Lister) ที่ออกแบบขึ้นเพื่อให้ทนทานต่อทุกสภาพ การอยู่ตัวของการย่อยสลายก๊าสชีวภาพนั้นจะทำให้การกำเนิดพลังงานอยู่ตัวด้วยเช่นกัน ดังนั้นจึงน่าจะเหมาะสมกับเครื่องยนต์ที่ใช้ไถนาหรือเครื่องยนต์แบบลิสเตอร์มากกว่าเครื่องยนต์ที่สามารถเชื่อมต่อกับอุปกรณ์อื่นๆได้ (เครื่องปั่นไฟ/ปั๊ม/เครื่องจักร)
ระบบเชื้อเพลิง
เครื่องยนต์ดีเซลไม่เหมือนกับเครื่องยนต์เบนซินตรงที่ไม่มีคันเร่ง แต่ใช้กัฟเวอร์เนอร์ (หรือเครื่องควบคุมความเร็วของเครื่องยนต์) ในเครื่องยนต์ที่ซับซ้อนขึ้นไป กัฟเวอร์เนอร์นี้สามารถทำงานได้ด้วยไฟฟ้า อิเลคโทรนิค หรือพลังงานน้ำได้ แต่เครื่องยนต์พวกควายเหล็กหรือรถไถนาจะใช้กัฟเวอร์เนอร์แบบธรรมดาแต่มีประสิทธิภาพที่ควบคุมด้วยกลไกลทั้งหมดๆ หน้าที่ของกัฟเวอร์เนอร์คือรักษาความเร็วของเครื่องยนต์ตามโหลดของเครื่องยนต์ (กัฟเวอร์เนอร์อันอื่นอาจรักษาโหลดของเครื่องยนต์ไม่ว่าความเร็วจะเป็นอย่างไรก็ตาม แต่อย่างที่กล่าวไว้คือมีความซับซ้อนกว่าและมีราคาสูงกว่ามาก) กัฟเวอร์เนอร์จะเป็นตัวควบคุมปริมาณเชื้อเพลิงเพื่อรักษาความเร็วตามที่กำหนดไว้แล้ว ความเร็วของเครื่องยนต์นั้นจะถูกปรับด้วยแร็คควบคุม ที่ถูกตั้งไว้ตามความเร็วที่ต้องการ ผู้ใช้ใช้แร็คควบคุมเหมือนการควบคุมคันเร่ง แม้ว่าหน้าที่ของมันจะต่างจากเครื่องยนต์เบนซินคือใช้ควบคุมปริมาณเชื้อเพลิง แทนที่จะใช้ควบคุมปริมาณอากาศ แต่ผลที่ได้ก็คล้ายกัน สิ่งสำคัญที่ควรคำนึงถึงคือ เมื่อเราแนะนำการใช้ก๊าสชีวภาพในระบบ เราจะทดแทนอากาศ “เฉื่อย” ด้วยส่วนผสมระหว่างเชื้อเพลิงและอากาศที่อัดระเบิด เพื่อการปรับเปลี่ยนด้านกายภาพที่เกี่ยวข้องกับขบวนการเผาไหม้ให้สมบูรณ์ โชคดีที่เราทุกคนไม่จำเป็นต้องเป็นผู้เชี่ยวชาญด้านความร้อนกับพลังงานกลก่อนถึงจะทำงานนี้ได้ ความจริงแล้ว ระบบนี้มีแนวโน้มที่จะสร้างสมดุลได้เองและอัตราการจุดระเบิดของเชื้อเพลิงและอากาศก็เกิดขึ้นเองอัตโนมัติ
ชนิดของเครื่องยนต์
ก๊าสชีวภาพไม่สามารถจุดระเบิดเองได้ภายใต้แรงอัด ดังนั้นจึงต้องใช้น้ำมันดีเซลจำนวนเล็กน้อยเพื่อการจุดระเบิด จากการค้นคว้าทางอินเตอร์เน็ตและจากการทดลองด้วยตนเอง อัตราส่วนที่เหมาะสมที่สุดที่ในการใช้ก๊าสชีวภาพเป็นเชื้อเพลิงน่าจะอยู่ที่ น้ำมันดีเซลร้อยละ 20 ต่อก๊าสชีวภาพร้อยละ 80 การเติมน้ำมันดีเซลเข้าไปนิดหน่อยมีความจำเป็นการหล่อลื่นของหัวฉีด ซึ่งถือเป็นหน้าที่อีกอย่างของน้ำมันดีเซล
ถ้าคุณต้องการให้เครื่องยนต์เดินด้วยก๊าสชีวภาพเพียงอย่างเดียว คุณจำเป็นต้องมี “เครื่องยนต์ก๊าส” (ไม่ใช่เครื่องยนต์เบนซิน) ซึ่งเครื่องยนต์ก๊าสนี้โดยพื้นฐานคือเครื่องยนต์ดีเซลที่จุดระเบิดด้วยประกายไฟ (spark ignition หรือ SI) ซึ่งตรงกันข้ามกับเครื่องยนต์ดีเซลที่ที่ใช้แรงอัดเพื่อการจุดระเบิดของเชื้อเพลิงและอากาศ เครื่องยนต์ก๊าสขนาดเล็กมีขายอยู่บ้าง แต่มักจะมีราคาแพงและหายากกว่าเครื่องยนต์ดีเซลธรรมดา เนื่องจากเครื่องยนต์มีระบบการจุดระเบิด จึงทำให้ค่อนข้างจะซับซ้อนกว่า ข้อดีของเครื่องยนต์ดีเซลคือความเรียบง่าย และไว้วางใจได้ในส่วนประกอบการทำงานที่เป็นกลไกทั้งหมด ซึ่งการใช้ระบบคอยล์, หัวเทียน, องศาจุดระเบิด, ฯลฯ ทำให้เกิดระบบที่ซับซ้อนที่ต้องมีการดูแลรักษาเพิ่มขึ้นและมีโอกาสที่จะเกิดความเสียหายได้มากกว่า
Figure 1. The diesel engine fuel system
ข้อมูลเบื้องต้นเกี่ยวกับก๊าสชีวภาพ
เนื่องจากระบบหัวฉีดที่มีแร็ค ก๊าสชีวภาพสามารถนำเข้าไปและถูกเผาไหม้ ในช่องรับอากาศของเครื่องยนต์ดีเซลโดยตรง ดังนั้นแร๊คจะถูกปรับโดยอัตโนมัติไปตามเชื้อเพลิงที่ใช้ (ภาพที่ 1) อาจมีการเปลี่ยนแปลงของ “ความเร็ว” เครื่องยนต์ไปเมื่อมีการปรับเปลี่ยนเชื้อเพลิงที่เป็นก๊าสชีวภาพ โดยเครื่องยนต์อาจมีการเพิ่ม และ/หรือ ลดรอบต่อนาที ซึ่งขึ้นอยู่กับ ก) สภาพของเครื่องยนต์ และ ข) สภาพของก๊าสชีวภาพ แต่สิ่งสำคัญคือไม่ว่าจะมีความเร็วหรือรอบต่อนาทีอย่างไร เครื่องยนต์ควรเดินต่อไปอย่างต่อเนื่องได้เอง
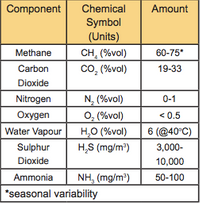
Table 1. Constituents of Biogas
Long-term Effects of Biogas on Engines
Although the majority of biogas constituents are benign, the long-term exposure of the engine’s material components to hydrogen sulfide (H2S) will be detrimental to the mechanical elements of the engine. If the working life of the engine is a consideration, the H2S should be removed from the gas (scrubbed). Other major components of biogas, such as water vapor (H2O) and carbon dioxide (CO2), do not cause any irreparable damage to the engine. However, CO2 is a large component of the gas and will make the ignition inefficient. Water vapor is also harmless, but if it condenses after use and is left for a long period of time, iron oxide (rust) will form on the cylinder components.
Engine Condition
In my initial experiments at the hospital in Lao PDR, the engine was in a poor state of repair. Equipment was not available to measure the compression ratio, but I estimated it to be as low as 13:1 or 12:1. The result of this was disappointing, as I was only able to achieve a maximum fuel ratio of 20:80 (20% biogas to 80% diesel).
Biogas Consumption Tests
I measured the ratio of the biogas:diesel consumption using a large syringe
Figure 2. Syringe for measuring diesel consumption, with ‘swirl chamber’ also shown.
Figure 3. Chinese-made laser tachometer for $25 did the job well.
mounted in the fuel line (Figure 2). The syringe was filled with a known quantity of diesel fuel. The engine was run and the speed measured using a tachometer (commonly referred to as a tacho - Figure 3).
Tachos can be difficult to source in some countries, and it was impossible to get one in Laos. I bought a Chinese-made laser tacho on e-bay for $25, which seemed to work well. The consumption of the known quantity of diesel (in the syringe) is timed using 100% diesel at a set engine run speed. Then the test is repeated by feeding biogas into the engine in an effort to use as little diesel and as much biogas in the mix as possible.
In my early experiments, I modified the air filter by inserting an inlet with a valve and a hose connector into the air filter housing (Figure 4). The biogas was then connected directly from the biogas digester to the air intake by a flexible hose. The bigger the hose, the better; in our case we used a ¾” hose with a ¾” valve. The engine should be able to start on biogas but, for the sake of practicality, I found it easier to start the engine on pure diesel and then open the biogas valve on the air filter.
During my early experiments, I also created and tested a ‘swirl chamber’ (Figure 5) in order to better mix the oxygen and biogas before combustion; I constructed this from a steel tube with a diffuser in the middle (Figure 5). The reason that you might use a ‘swirl chamber’ is that methane molecules are tiny compared to those of oxygen. In some online articles, a ‘swirl chamber’ is recommended, and they are used in some modern cars. In my latest experiments, I have not found them to make a difference in performance. However, they might help in some instances, and you might consider trying one if you are having problems with efficient combustion.
Figure 6. Old diesel engine in poor condition.
Figure 8. Correct inlet point for biogas marked by white X on air inlet.
The above experiments were undertaken using an old diesel engine in poor condition (Figure 6). Another test was undertaken using a relatively new single cylinder Kubota engine (Figure 7). The results were more impressive using the new engine, because the engine ‘took off’ as soon as the biogas valve was opened. The rack was adjusted to a point where the engine tone (speed) was similar to that of the engine running pure diesel. The resultant smooth operation of the engine on biogas was obtained with a ratio of approximately 80% biogas to 20% diesel fuel mixture.
The biogas pressure to run the diesel engine does not need to be high, and the gauge we were using was not of high quality, but I estimated the biogas pressure to be at about 10 kPa (about 1.5 psi). The action of the engine will be enough to draw the fuel into the system, so a pressurized system is not required to run a diesel engine.
The engine was only run for a short period of time, because it was consuming an alarming amount of gas.
Figure 9. Modification for air inlet.
Location of Gas Inlet
Be sure to introduce the gas into the engine at the correct location. In my experiments, I introduced the gas into the air filter. After trialing this several times and speaking to others who have undertaken similar experiments, I realized that this was incorrect. The biogas inlet should be placed in the air intake manifold, just before it enters the engine (Figures 8 & 9). You can attach the biogas feed to this intake by cutting a hole and welding a threaded socket onto the inlet pipe, as shown in Figure 9.
The Lab at km 19
I did another research project with LIRE, this one to calculate the amount of energy that could be generated from a known input of feedstock. The lab was located at a pig farm just outside Vientiane at km 19. The farm also distilled a local rice whiskey called ‘Laos Laos’. The biogas produced by the pig farm was used for cooking and to fire the stills. They then used the ‘mash’ to feed to the pigs. This almost created a complete cycle of inputs and outputs, although in reality there were more inputs than just mash and biogas.
By measuring both the inputs and the outputs of the biogas production, we could calculate how much manure (in this case pig manure) would be required per kWh of energy produced using a diesel engine running on a mixture of diesel and biogas. The ‘lab’ consisted of an 8 m3 fixed-volume underground biogas digester. After production, biogas was fed into a 5 m3 biogas balloon for storage. For the power output, we used a small 4.8 kW single-cylinder Chinese-made engine. We measured output power using a ‘Prony brake’ mounted on the output shaft, a simple forerunner to the modern dynamometer.
[Note: Details of the Prony brake have not been included in this report. If more information on the ‘Prony Brake’ is desired, please contact the author.]
As part of our trials in Vientiane, we tested the effectiveness of ‘scrubbing’ the gas before it reached the engine. With the tests, we hoped to determine the most efficient and practical method of scrubbing the gas in a rural context (Figures 10 & 11).
Figure 10. Biogas lab schematic
Figure 11. The biogas ‘lab’
Biogas Scrubbing
I know of two effective and accessible ways of removing, or ‘scrubbing’, H2S (Hydrogen Sulfide), both of which can be applied using appropriate technology. Industrial scrubbers do exist, but their cost and availability would probably rule them out in a rural context. For an acceptable quality of gas, you will want less than 100 ppm (parts per million) of H2S in the biogas. Generally speaking, it will require more scrubbing than you might think.
Scrubbing Using Sodium Hydroxide
Sodium Hydroxide (NaOH), better known as ‘Caustic Soda’ or ‘Lye’, is a
12. Water tower schematic.
Figure 13. Water tower with gas pump and meter.
Figure 14. Filing the water tower. Note use of safety equipment.
comprehensive scrubbing medium that will remove CO2 as well as H2S. Sodium hydroxide is widely available even in remote rural communities, and can usually be purchased at a local building supply store. In order to scrub biogas with sodium hydroxide, you will need to build a ‘water’ tower; this can be constructed from locally available materials (Figures 12-13). In the tower, the gas is bubbled through a solution of water and Sodium hydroxide at a ratio (by weight) of 3:1 water to NaOH. The gas is pumped through the water tower into a manifold that has a series of small holes (Figure 12). The idea is to create bubbles that are as small as possible, thus increasing the surface area of the gas as it is passed through the solution of water and sodium hydroxide. A chemical reaction occurs, causing the H2S and CO2 to precipitate out and form a slurry at the base of the tower.
When using this approach, we became aware of serious drawbacks to the process:
- The design of the water tower made it awkward and cumbersome, both to get the solution in and to get the dilute with the slurry out. Although in the end, the biogas was scrubbed of H2S and CO2, we were left with a toxic slurry of which to dispose.
- Handling caustic soda is dangerous, and protective gear (gloves and glasses) MUST be worn (Figure 14). Safety equipment will be much harder to access than caustic soda. Also, there are potential cultural obstacles to overcome in the use of PPE (Personal Protective Equipment). Note: it is handy to have a bottle of vinegar on hand, because vinegar is acidic; if caustic soda is spilled on the skin, vinegar can be applied to neutralize the strong alkaline.
- The biogas must be pressurized enough to be able to push the gas through the water tower (i.e. there must be enough ‘head’ to do this). In normal operation, the pressure in the biogas balloon is likely insufficient to overcome the head; therefore, an additional gas pump must be added. In a rural location there might not be access to 240V mains power or a gas pump to add the extra pressure needed to use the water tower.
In our experiments, we circulated the 5 m3 of biogas through the tower and back into the storage balloon. Although final readings weren’t taken, we estimated that this would take 10 hours to complete the scrubbing cycle, and result in several kg of toxic slurry.
Scrubbing Using Iron Oxide (Rust)
An iron oxide (rust) scrubber is the usual ‘appropriate’ method for scrubbing biogas, because this kind of scrubber is simple to create. Rust consists of
Figure 15. Schematic of iron oxide scrubber.
hydrated iron oxides (Fe2O3•nH2O) and iron oxide-hydroxide (FeO(OH)•Fe(OH)3). As the gas is passed over the rust, a chemical reaction occurs, and the H2S precipitates out of the biogas (Figure 15). Unlike the sodium hydroxide scrubber, however, this method does not scrub the CO2.
The main challenge with this method is accessing steel or iron as a feedstock for the scrubber. Ideally, one would look for the shavings from a machine shop, often referred to as ‘swarf,’ ‘shavings,’ or ‘filings.’ Old ball
Figure 16. Iron Oxide gas scrubber.
bearings are ideal, as they have a large surface area to volume ratio, but they may be difficult to acquire in any useful quantities. Fine particles of steel ‘filings’ are not useful because the gas must be able to pass through the tube packed with the filings. Once the swarf has been acquired, it must be allowed to rust, with two or three weeks of exposure to the elements. (It is quite possible that the swarf will have been oiled originally to prevent the base material from rusting, so any swarf that is acquired must first be thoroughly degreased using a soap solution). After a few weeks of exposure to the elements, there should be a generous coating of rust on the swarf. The swarf should then be packed into a PVC tube (I used a tube that was 1.4 m long with 75 mm diameter) with an outlet and inlet at either end (Figures 16, 17). A couple of perforated plates helped with the assembly by creating a column of swarf in the PVC tube (Figure 18). The swarf in the column allowed the gas to pass freely, but had enough surface area for the iron oxide and the H2S to react. I suggest using removable end caps, as they will need to be removed to change the swarf.
The only real operating issue that I found with this method was the difficulty of making the tube air/gas tight. In the end, I concluded that, because of the low pressure, very little of the gas would escape. Unlike the sodium hydroxide method, no gas pump was needed to force the biogas through the swarf. I measured the effectiveness of the scrubbing afterward by bubbling the gas through a lead acetate solution, and measuring the amount of resulting lead sulfide (i.e. the sulfur not removed during the scrubbing) (*For details about the lead acetate test, please contact the author). Based on the lead acetate test, I concluded that four further stages of scrubbing would be required to remove all sulfur dioxide. Both approaches would require feasibility studies.
Scrubbing the Water Vapor
Although water vapor is not problematic for the ignition process, the introduction of water vapor into the cylinder could cause condensation and would promote rusting. Therefore, it is considered advantageous to add a ‘water trap’ before biogas enters the engine.
A crude water trap can be made using a steel tube with an inlet at one end and an outlet at the other. The steel tube must be placed in a location that is cooler than the gas in the tube, thus causing the water vapor to condense onto the inside of the tube. How this will be achieved depends very much on locally available cooling sources. Cooling sources such as underground thermal cooling, flowing water, etc. may be very difficult to find in rural situations. The tube needs to be about 6 meters long and must also have a drain cock to remove the condensed water. In my experiments, no ‘cooling source’ was available, so I decided to not remove the water vapor. Even without water vapor removal, the biogas was combusted in the engine without problem. However, longterm usage of un-scrubbed biogas in diesel engines may result in rusted cylinders and mechanical failure.
How Much Power can be Produced Using Biogas?
In many respects, the production of biogas is more of an art than a science. There are many variables to consider. When the gas is being used for cooking, the vagaries of biogas are mainly masked by its crude conversion (by combustion) to heat and light. When biogas is used as fuel for an engine, variations become more apparent and significant. Keep this in mind when reviewing results from tests of biogas as an engine fuel (as I have outlined below). In other circumstances, with other methods of biogas production and feedstock utilization, a completely different set of results might be obtained. Use the following results only as a rough guide.
Data from Tests and Empirical Results:
1 kg manure = 60 - 100 liters of biogas
An estimated 550 liters of CH4 are required per kWh of power produced at engine output shaft
Typically, biogas contains 60% methane on average; meaning 900 liters of raw biogas would be needed per kWh of energy
So 9 - 15 kg of manure would be needed per kWh of electricity
In Real Terms
If you ran a 10 kW generator for 3 hours, the amount of energy produced would be 30 kWh, requiring 270 - 450 kg of manure to be fed into the biogas digester as the feedstock.
Remember that this is the output from a diesel engine. For power generation, the output shaft needs to be hooked up to a generator via either a belt and pulley or chain and sprockets. Please be aware that electromagnetic resistance in the generator windings will also require energy input to overcome, again reducing the overall efficiency. For small generators (up to say 50 kW), allow a further 15% reduction in usable power.
Is Biogas Practical for Power Generation?
It is possible to use biogas for power generation. However, a number of practical considerations need to be addressed. Running an engine on biogas requires a lot of biogas, which requires a lot of feedstock, and hence a lot of labor and infrastructure. The technical requirements, materials needed for scrubbing, and other inputs require a significant technical and labor investment.
I conclude that using biogas to power a diesel engine for electrical generation and/or mechanical work should be considered as a last resort rather than a first option, especially if grid power is available.
YouTube video: http://www.youtube.com/ watch?v=nKFe7N7Q4iE
[Gordon Hirst: Engineering consultant & appropriate technology specialist; Chief Engineer, Maejo University School of Renewable Energy. gordon.e.hirst@gmail.com]