Figure 1: ‘Fermented Banana-Based Feeds’ are made weekly here at the ECHO Asia Farm. ECHO’s Agricultural Specialist, Chai, shows us the materials needed to make the banana stem base.
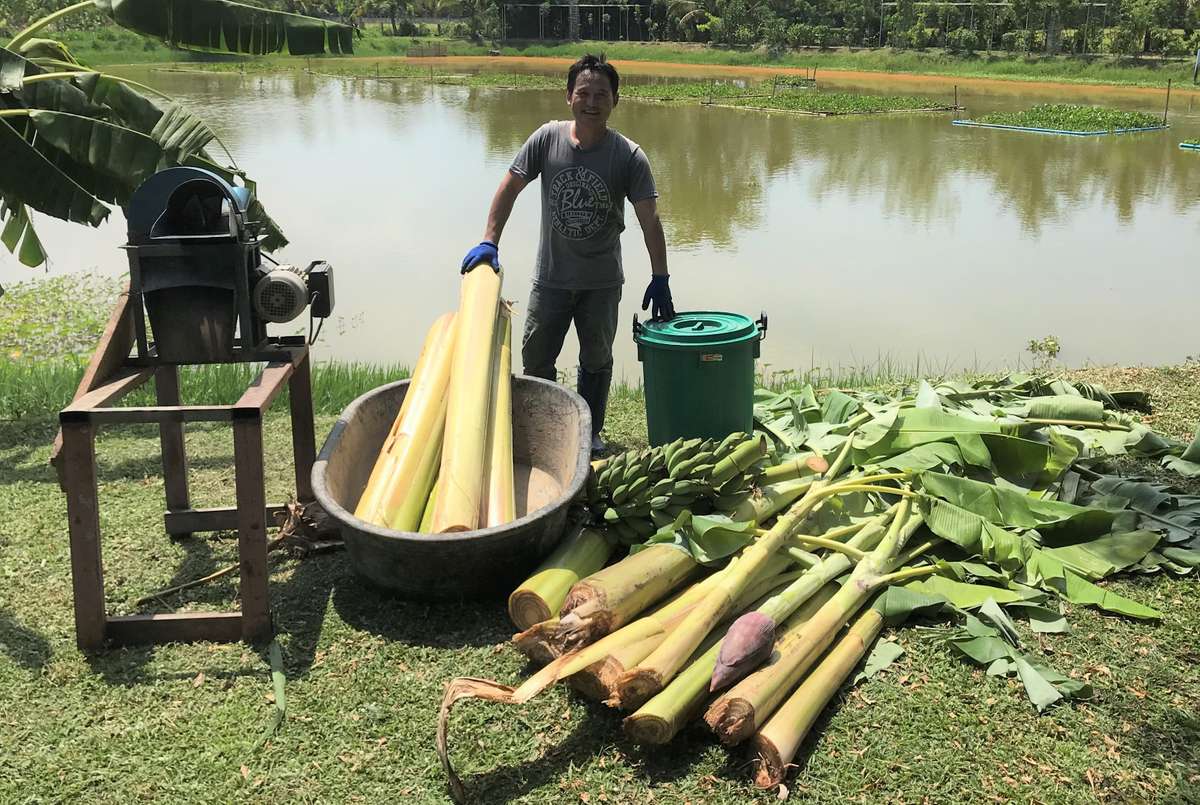
This article is from ECHO Asia Note # 42
[Editor’s Note: Based on feedback from the network, we would like to provide and promote further discussion on each article published. For additional questions, comments, or suggestion on this topic we invite you join to our ECHOcommunity ‘Conversations Forum’ where we have opened a new conversation topic called ‘Making On-Farm Feeds - Asia Note #42 Discussion’]
Introduction to Fermented Banana-Stem Feeds
The integration of livestock on the smallholder farm is often a key component to the long-term sustainability of the farm, specifically by means of critical nutrient cycling. Livestock play a unique and critical role on the farm, transforming plant and waste materials into important sources of energy, either for consumption on the farm, or for sale beyond it. As omnivores, pigs are one of the most efficient converters of on-farm ‘waste’, transforming materials unsuited for human consumption, into meat, manure, and income.
On the ECHO Asia Farm we seek to create our own ‘Farm-Generated Feeds’ for the purpose of leveraging the materials we have available to us, while bringing down our costs of livestock production. In addition to the meat and income produced through our cows, pigs, chickens, and fish, we also value them for their manure, which we compost and use in crop production among other things.
To make on-farm feeds we recommend utilizing locally available resources (on the farm or within the vicinity), with special attention to materials that could be considered ‘waste products’ or ‘under-valued’. At the ECHO Asia farm we use for our base ingredient our most readily abundant material, the banana tree. For the remainder of this article we will focus on the production and benefits of ‘banana-based pig feeds’, produced primarily form the stem of the banana tree. These stems are fermented to break down and increase digestibility and are subsequently mixed with various other low-cost raw materials that are locally available, including rice bran, corn meal, and fish meal, etc… (see Table 1.) This is not a new technique, having long been adopted on many smallholders farms in this region, but does have room for improvement
How we make our On-Farm Feeds at ECHO Asia
1. Selecting the banana stem
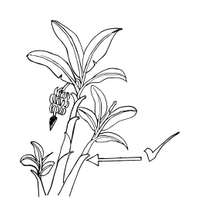
Not all banana stems are equal in terms of nutritive value. We recommend harvesting younger stems for making feed when possible (Figure 2). At this stage of growth, stems have not yet diverted their energy and nutrition into fruit production, and remain tender and digestible. We plant the ‘namwaa’ (กล้วยน้ำว้า) banana variety (Musa sapientum L) for our feed purposes.
2. Chopping
Leaves are cut off from the stem (used for goats and cattle) and only the stem is utilized for pig feed. Using a chopping machine, stems are fed through to produce chopped pieces anywhere from 2-5cm in length (Figure 3.1). The smaller the piece, the more easily they will ferment and breakdown. This is helpful for pigs which are monogastric animals (single stomach), unlike ruminant animals like cows (multi-stomach), that are more efficient in breaking down plant fibers.
3. Fermentation
We employ a short fermentation; whereby chopped banana stems are fermented only 3-4 days (Figure 3.2). Molasses and mineral salt are mixed with chopped banana stems then packed and sealed into an airtight bin and left to ferment. Without fermentation, banana stems may not have much nutritional value, but this process can introduce beneficial microorganism populations that become a bypass protein source for the pigs (more research needed here).
4. Bulking Up with Other Ingredients
Fermented banana stems alone hold low nutritional value and must be mixed with other higher quality ingredients for a proper feed ration (Figure 3.3). Testing of our fermented banana stems resulted in a 6% crude protein content. Table 1 summarizes the ingredients we mix. Note: these ingredients are the resources most available and affordable to us based on the location of our farm and may not be ideal in other locales.
Research Trials: On-Farm Feeds vs. Commercial Feed
For several months, the ECHO Asia Farm has been trialing our fermented banana stem feeds with our local black pigs to see how they compare to commercial feeds in a small production system. The objective was to assess the overall price of producing our own feeds while maintaining comparable weight gains of pigs fed with commercial feed. One group of pigs was fed commercial feed, while the other group was fed the On-Farm Feed mix; all pigs belonged to the same litter and were split evenly according to initial weight and gender. Pigs were weighed every 2 weeks.
Table 1 is a summary of our Farm-Generated Feed rations based on three different protein targets for different growth stages. The goal was to produce a feed from on-farm and locally available materials that might compare to a commercial feed in terms of nutritional composition and overall cost. Fermented banana stems were used as the base ingredient while other materials were either harvested from the farm or purchased locally.
It is important to note that banana stems were assigned a value (despite being free on our farm), in order to account for the labor involved in their production. It is important to account for, and value, the added labor of any smallholder farmer that might adopt these practices.
The cost of making on-farm feeds with the above formulas were much cheaper to produce per kilogram (Table 2) when compared to purchased commercial feeds. However, due to the high moisture content of the fermented banana stem portion of the feeds, it was necessary to feed roughly 50% more of the On-Farm Feeds in order to retain comparable dry matter contents with that of the commercial feeds (Table 3). Note: moisture content of the fermented banana stems alone was roughly 90%, but the complete ration averaged closer to 50% moisture content once banana stems were mixed with other ingredients.
Feed formulas were adjusted depending on growth-stage of the pigs, providing a higher protein feed as pigs were younger and faster growing, and lowered as pigs grew older. Table 3 summarizes the rates of feed provided to pigs at each stage, with rations increasing as pig grew older and protein contents were lowered.
Results from ECHO Asia Feeding Trials
Results from these trials showed that pigs raised on commercial feed will take approximately 147 days to reach market weight (70kg target) and will consume approximately 105 kg of feed (calculated once piglets are 9 weeks old). We calculated that the cost of feeding over this period to be 1733 THB per pig (see Table 4). Pigs raised on the farm-generated feeds gained weight more slowly (only reaching market weight after 159 days) and therefore consumed roughly 2 weeks more worth of feed, for an overall total of 189kg of feed per pig.
Although on-farm feeds were cheaper to produce per kilogram, these had to be fed at a higher rate (both daily and over life of the pig), and therefore resulted in a higher overall cost to the producer, in this case 1930 THB. These results are a good reminder that not all feeds are created equal, and considerations need to be made based on nutritional value and not volume alone when comparing farm feeds to commercial feeds.
Feed Conversion Ratios
A Feed Conversion Ratio (FCR) is a method typically used to define how efficient an animal is at converting feed into body weight. For example, a cow might require 8 kg of feed to put on 1 kg of body weight, while a fish may only need 1.5 kg of feed to put on 1 kg of body weight. This ratio can also be used to determine the efficiency of a feed, when used across the same animal type, as was the case in our pig feeding trials.
Using the data collected during these trials we were able to estimate an average FCR of 2.7 for our commercial feeds, and an average FCR of 4.3 for the on-farm feed (Table 4). This highlights the fact that not all feeds are created equal and that the on-farm feeds, with a lower conversion ratio, must be fed in larger amounts in order to compare. Going forward the goal will be to improve the FCR of our on-farm feeds through the inclusion/substitution of other high quality ingredients.
Recommendations
These results indicate at first glance that commercial feeds are the superior option and that there will be a higher cost to farmers producing feeds on the farm, but we feel this farm-generated feed approach can be of great value to farmers living in remote areas where commercial feeds may be more difficult to obtain. There are also significant cost savings opportunities as additional ingredients can be identified and substituted for the purchased ingredients listed above.
There is significant potential for pig producers to begin substituting the ingredients listed with materials and resources located on the farm, thereby lowering costs. This is especially true for farmers already producing some of the ingredients listed, such as the rice bran, corn meal, and even fish waste. If any, or multiple, of these ingredients can be produced on farm at a lower cost than to purchase it, the overall savings can surpass a commercial feeding strategy and become more profitable.
Perhaps one of the largest possible areas for profit increase would be the potential of marketing pigs fed with on-farm feeds as ‘organic’ or ‘natural’. Assuming demand for such meat, there lies significant potential in increased profit margins should the production or certification requirements be met!
We acknowledge the location of our ECHO Asia Farm being on the outskirts of a major urban center, with ready access to products such as rice bran and fish meal and understand that small upland farmers may not easily obtain these ingredients. The formulas used on the ECHO Asia Farm are NOT prescriptive and should only be used as one example of an on-farm feed formula. We encourage you to seek out the unique resources available to you in your locale, and to experiment with what materials you can acquire. If one of the above listed materials is not available, or is too expensive, it can be substituted for another material of similar nutritional value. Numerous other high-protein options exist including, copra meal, soy meal, insect meal, bone meal, azolla (Azolla caroliniana), moringa (Moringa oleifera), fish amino acids (FAA), and more.
Keep in mind also that a transition from commercial feeds to on-farm feeds may not be feasible, and a hybrid system may work best for your production system. It is not uncommon to employ both strategies simultaneously and to supplement either feed with the other. A 50-50 split between commercial feed and on-farm feed, or any combination of the two is a good option to consider in the beginning. However, adopting a stricter farm-generated feed strategy may provide additional options that may not have existed before, and marketing pigs to new markets as ‘organic’ or ‘natural’ may have potential to fetch a higher price.
The illustration on the previous page (Figure 5) summarizes more simply some of advantages and disadvantages of both feeding strategies:

More Information Coming Your Way!
At the time of writing this article, the team at the ECHO Asia Farm have already begun another round of pig feed research to determine the cost-benefits of varying amounts of daily on-farm feeds.
Stayed tuned for updates! We plan to continue testing our on-farm feeds, to improve their nutritional make-up, cost, and practiciality to smallholder farmers in Asia.
Additional Resources
Mikkelson, O. 2019. Integrating Hogs into the Smallholder Farm and the Creation of Hog Feed. In: Animal Integration & Feeding Strategies on the Tropical Smallholder Farm. pp. 41-55. ECHO Asia Impact Center, Chiang Mai, Thailand